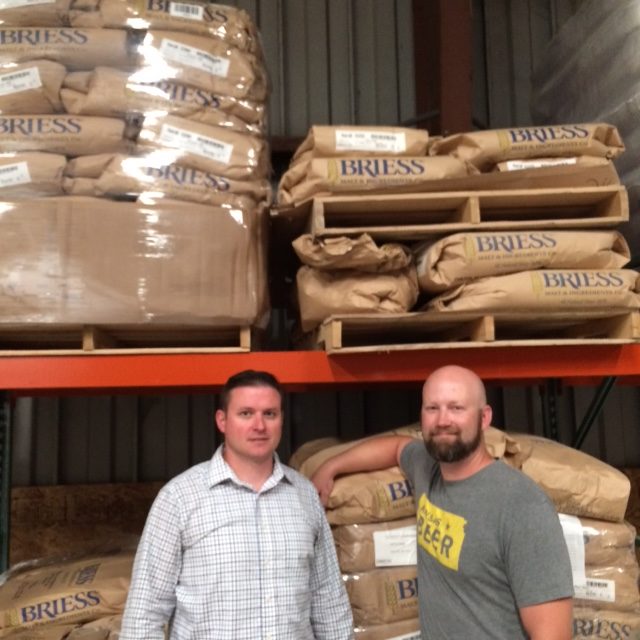
Notice to all small brewers: When it comes to organizing your brewery’s malt storage, plan for success.
One of the most common situations I run into is the lack of palleted malt storage space. Larger, more established breweries have figured this out, but smaller breweries seem to struggle with dedicating adequate space for malt storage. I’ve seen brewing companies that are on their second brewery and still don’t leave adequate room for malt storage.
I like to remind smaller breweries that as they grow, there will be a point in time where they can start purchasing malt directly from the Malthouse. Often the dealmaker is two-fold.
- The ability to store somewhere between 6,000 and 12,000 lbs. of malt, if not more.
- Being able to purchase in these sorts of quantities often allows favorable pricing from the supplier and helps amortize the cost of shipping over many pounds of malt.
Here are a couple of my personal observations. Many small breweries these days have silos, many do not have forklifts unless their business plan is strongly slanted towards distribution.
Disclosure: As all brewers know, malt inventory is a bit of a moving target and the below examples are just that.
How much storage do you really need?
Example 1:
A 3,000 Bbl./yr. brewery will use about 195,000 lbs. of malt per year, or 32,500 lb. every two months or roughly 16 pallets or 32,000 lbs. In this scenario, the use rate would be two pallets per week. If your reorder point is 8 pallets in inventory, by the time your shipment arrives in a couple of weeks, there will be a need to have the ability to store around 20 pallets of malt or 315 sq. feet + room to move and clean.
Example 2:
Let’s say you are fortunate enough to have a silo and need only to store 20% of your annual usage in specialty malts. This 20 % may include special base malts, lightly kilned products along with roasted and caramel goods. If that is the case, you’ll need to store roughly ~6,500 lbs. every two months. Let’s call this 8,000 lbs. or 4 pallets. If your reorder point is around 2 pallets, then your storage should accommodate around 5 pallet positions. This example single stacked equals roughly 79 sq. feet + forklift backing and turning space while transporting the pallet of 12’ to 13.’ (If you are a user of malted wheat that is not in bulk, this percentage could go up.)
Possible configurations to minimize your footprint are:
Single Stack
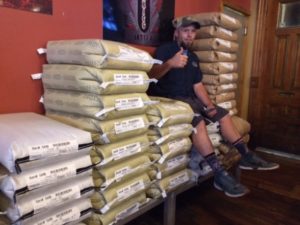
Allow 15.74 sq. feet per pallet as a footprint. (This allows a couple of inches all around the pallet for sanitation inspection.)
Pallet Racking
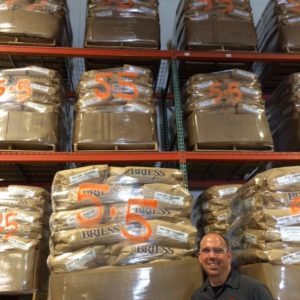
This requires a forklift to stack malt. They are generally 8-foot-wide sections with each vertical section being about 64” in height. The depth is typically 48”. 2 pallet positions side by side per 8” section of pallet racking. Stacking height is determined by building height and proper safety and engineering design.
Super sack stations
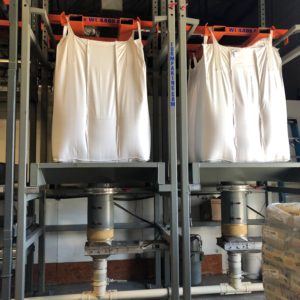
They are a generally about 64” wide per station, require a vertical clearance of about 11’ and are 48” deep. Super sack stations require a forklift or mechanical lifting of the sack into position and proper engineering for safety.
I think the moral of the story is to plan for success and have a feel for how much space is required to store palleted malt. When in doubt, round up without being wasteful and have a plan in place. Chances are the plan will change, but at least you have thought about it and hopefully will still end up with adequate room to safely store and move around your malt storage area.
Cheers,
Dan