Bins are pretty simple pieces of equipment, just vertical walls for containing the grain with no moving parts. How do they operate? New malt goes in the top and the old malt comes out the bottom — pretty simple, right? Actually, that turns out not to be the case most of the time. Over the years, many customers have run into problems because they didn’t fully understand how malt moves in their bins. So, how does grain move?
Grain flows out of a bin mainly in one of two ways — mass flow or funnel flow.
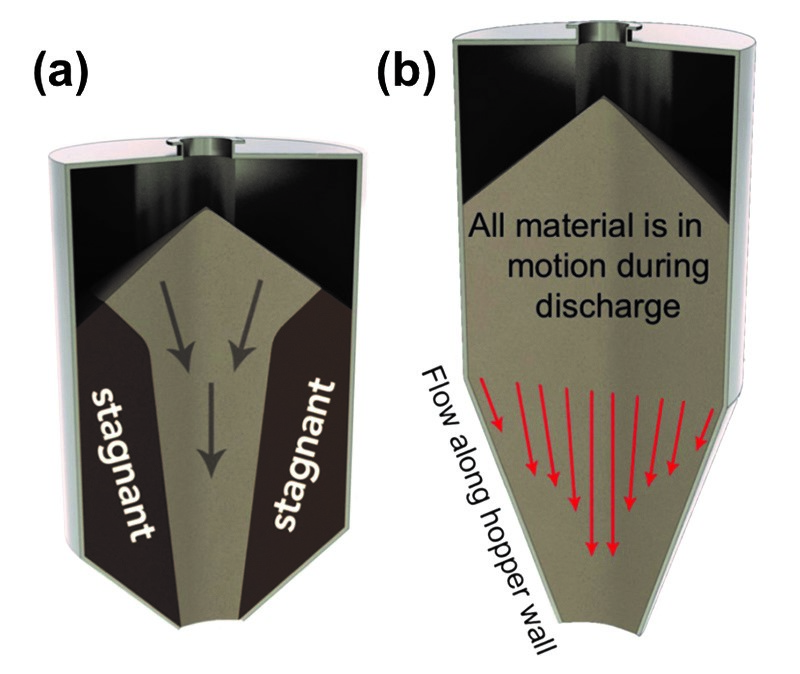
Funnel Flow Bins
In funnel flow bins, the material immediately above the bin opening falls into the opening and the material on top of that follows. This creates a thin moving column of material in the bin above the opening, causing a hole to form in the grain mass at the top of the bin. Grain at the top will collapse into the hole, forming an inverted cone that looks like the Sarlacc from Star Wars: Return of the Jedi. Anyone who has ever watched a bin empty in this way instantly understands why it’s so dangerous to be on grain that is moving. Anything on top of the grain tumbles down the cone and is swallowed by the hole at the bottom. Material swallowed by the cone will funnel through the non-moving grain mass below and exit first (see video).
Video Courtesy of Briess Technical Services Associate Scott Heimerl
If a new batch of malt is delivered on top without emptying, this new material will follow this same pattern and come out of the bin first, before the older malt below. In this way, funnel flow bins act as a first in/last out system. This is the opposite of good manufacturing practice for raw material handling. Material in the stagnant zone will not move and can indeed be in the same spot for years if the bin isn’t emptied. This can lead to moisture pick up, increased risk of contamination, loss of enzymes, and flavor issues in malt. Additionally, when the bin is finally emptied — the brewer isn’t seeing the malt that was loaded into the silo last but is seeing some random lot from several years ago.
Mass Flow Bins
Bins exhibiting mass flow behave the way most people think they should. New malt goes on top, older malt comes out the bottom. In mass flow bins all the material moves downward when the bin is emptying (see video). They are self-cleaning as the abrasive grain moves along the walls each time the bin is emptied. Mass flow bins allow for first in/first out removal of the grain.
Video Courtesy of Briess Technical Services Associate Scott Heimerl
Despite these advantages, they have some cons as well.
Mass flow bins are typically more expensive. Normally they have a steep cone angle of about 60 degrees, which requires a bigger cone needing more material. More importantly, they are also taller because of this — which requires higher ceilings in the buildings and taller (longer) grain handling equipment. Many breweries have mass flow bins, but almost all grain elevators have funnel flow bins, most with flat bottoms because of cost. In mass flow bins, there is less mixing between batches or lots so changes between them will be more abrupt. Also because the material on top isn’t mixed in, they are prone to a phenomenon known as air classification. During filling, the falling grain creates air currents inside the silo that suspend the light husk material in the air. After filling, the light material settles on the top of the grain in a layer. When filling a second time — if the silo isn’t emptied — this layer is quickly suspended in the air and combined with the light material from the second fill. Over time, the bin can have a layer on top several inches thick. When the bin is finally emptied, the brewer will see large amounts of husk coming out of the silo. I’ve had customers who were unprepared for this phenomenon send me samples from their last brew that are 70% husk and others report that their extract went down to 50%.
Funnel Flow
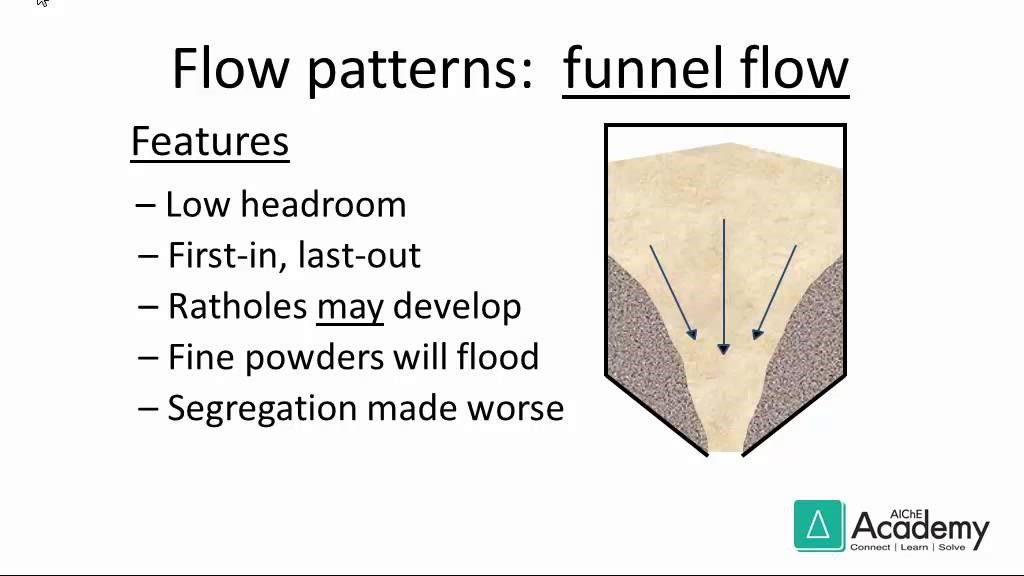
Mass Flow

What causes different behavior?
The frictional forces between individual grains as well as against the bin wall cause resistance to flow and create compressive forces within the grain mass that can “lock” it into place. The higher the friction, the greater the likelihood that funnel flow will occur.
How do you know which type of flow you have?
Any silo with a cone angle smaller than 40 degrees will be “funnel flow” unless it has some sort of flow-modifying device inside. Normally, cone angles >60 degrees will give mass flow — though they can be funnel flow if they are square or if there are problems with the feeding mechanism emptying the tank. It is relatively easy to determine which you have, though if you look at the top of the grain in your bin after withdrawing grain from it. In bins exhibiting funnel flow, the top of the grain will form an inverted cone where the center has collapsed into the funnel. In mass flow bins, the grain will show a hump below the point where it was filled. This hump will normally flatten out slightly as the silo is emptied.
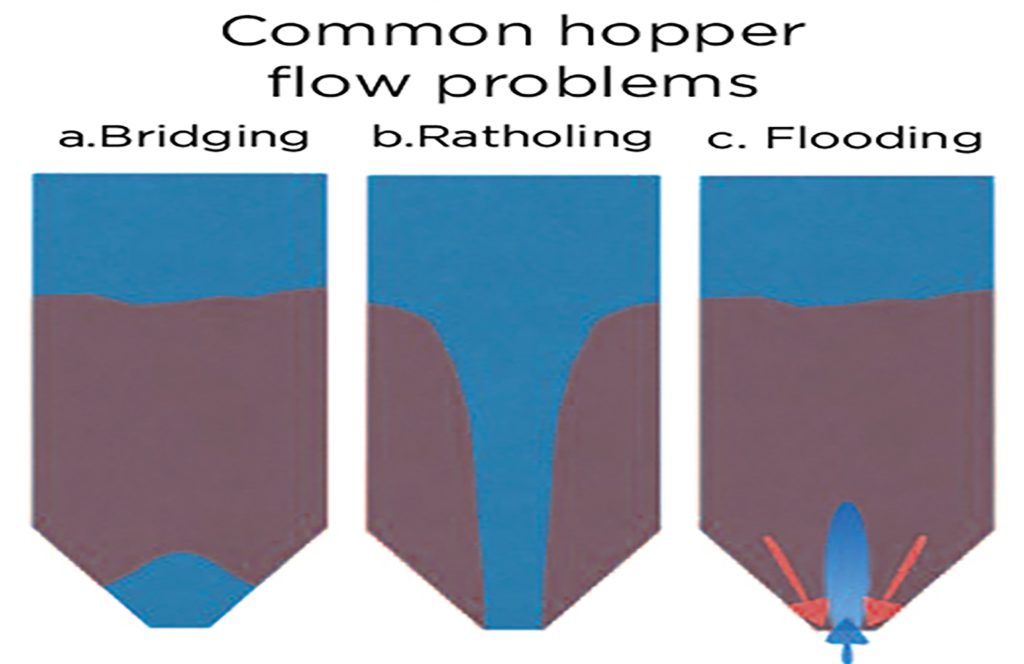
Don’t let bin problems happen to you!
The way to prevent brewing issues caused by bin storage is to understand the problems and empty the bins completely with some frequency — usually annually. Normally brewers will fill the gap with a few totes of pre-ground or whole kernel malt to avoid any disruption to their brewing during the emptying. Paying careful attention to the last material coming out and making adjustments to the brewing process where needed will prevent unexpected problems.